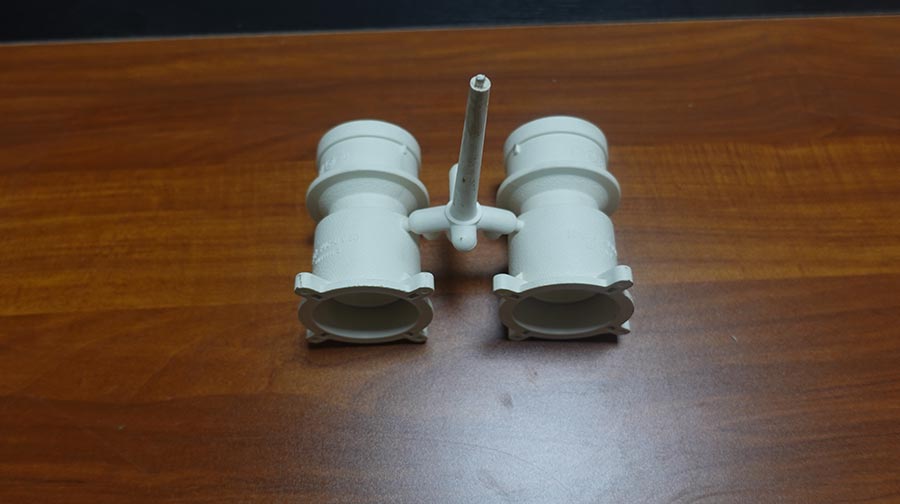
塑件的注塑成型工艺过程主要包括填充——保(bǎo)压——冷却——脱模(mó)等4个阶段,这4个阶段直接决定着(zhe)制品(pǐn)的成型质(zhì)量,而且这4个阶段是一个完整的连续过程。
1、填充阶段(duàn)
填充是整个注塑循环过程中的一步,时间从模具闭合开始注塑算起,到模具型腔填充到大约95%为止。理论上,填充时间(jiān)越短,成型效率越高,但是实际中,成(chéng)型(xíng)时间或者注(zhù)塑速度要受到很多条件(jiàn)的制约。
高速填充。高速填充时剪(jiǎn)切率较高,塑料由于剪切(qiē)变稀的(de)作(zuò)用而存在粘度下降的情形,使整体流动阻力降低;局部(bù)的粘滞加(jiā)热影(yǐng)响也(yě)会使固化(huà)层厚度变薄。因此在流动控制阶段,填充行为往往取决于待填(tián)充的体积大小。即在流(liú)动控制阶段,由于高速填充,熔体的剪切变稀效果往往很大,而薄壁的冷却作用并不明显,于(yú)是速率的效(xiào)用占了上风。
低(dī)速填充。热传导控制低速填充(chōng)时,剪切率(lǜ)较低(dī),局(jú)部粘度较高,流动阻力较大(dà)。由于热塑料补充速(sù)率较慢,流动较为缓慢,使(shǐ)热传导效应较为明显,热(rè)量迅速为(wéi)冷模壁带走。加上较少量的粘滞加热现象(xiàng),固化层厚(hòu)度较厚,又进一(yī)步增(zēng)加壁部较薄处的流动阻(zǔ)力。
由于喷泉流动的原因,在流动波前面(miàn)的塑料高分子链排向几乎平行流(liú)动波前(qián)。因此两(liǎng)股塑料熔胶在交汇时,接触面的高分(fèn)子链互相平行;加(jiā)上两股熔胶性质各异(在模腔中滞(zhì)留时间不同,温度(dù)、压力也不(bú)同),造成熔胶交汇区域在微观上结构强度较(jiào)差。在光线下将零件摆放适当的角度用肉眼观察(chá),可以发现有明显的接合线产生,这就(jiù)是熔接痕的形成机理(lǐ)。熔接痕不仅影响塑件外(wài)观,同时由于微观(guān)结构的松散(sàn),易造成应(yīng)力集中,从而使得该部分的强度降低而发生断裂。
一般而言,在(zài)高温区(qū)产生熔接的熔接痕强度较佳,因为高温情形下,高分子链活动性较佳,可以(yǐ)互相穿透缠(chán)绕,此外高温度区域两股熔体的温度较为接近,熔体的(de)热性质几乎相同(tóng),增加了熔接区域的强度;反之(zhī)在低温区域,熔接强度较差。
2、保压(yā)阶段
保压阶段的(de)作用(yòng)是持续施加压力(lì),压实(shí)熔体,增加塑料密(mì)度(dù)(增密(mì)),以补偿塑料的收缩(suō)行为。在保压过程中,由(yóu)于模腔中已经填满塑料,背压较高。在保压压实过程中,注塑机螺杆仅能慢慢地向前作微小移动(dòng),塑料的流动速度也较为缓慢,这时的流动称作保压流(liú)动。由于在(zài)保压阶段(duàn),塑料受模壁冷却固化加(jiā)快(kuài),熔体粘度增加也很快,因(yīn)此(cǐ)模具型腔内(nèi)的阻力很大。在保压的后期,材料密度持续(xù)大,塑件也逐(zhú)渐成型(xíng),保压阶段要一直持续到浇口固化封口为止,此时保压阶段的模腔压力达到高值。
在保压阶段(duàn),由于压力相当高,塑料呈现部分可(kě)压缩特性。在压力较高区(qū)域,塑料较为密(mì)实,密度较高;在压力(lì)较低区域,塑(sù)料较为疏松,密度较低,因此造成密度分布随位置(zhì)及时间发生变化。保压过程中塑(sù)料流速极低,流动不再起作用;压力为影响保压过(guò)程的主要(yào)因素。保压过程中塑料已经充满模腔,此(cǐ)时逐渐固(gù)化的熔体作为传递压力的介质。模腔中的压(yā)力借助塑料传(chuán)递至模壁表面,有撑开模具的趋势,因此需要适当的锁模力进行锁(suǒ)模。涨模(mó)力在正常情形下会微微将模具撑开,对于模具的排气具有帮助作用;但若涨模力过大,易造成成型品毛边、溢料(liào),甚(shèn)至撑开模(mó)具。因此在选择注塑机时,应选择具有足够大锁模力的注塑机,以防止涨模现象并能有效进行保压。
3.冷却阶段
在注塑成型模具中,冷却系统的设计非常重要(yào)。这是因为成(chéng)型塑料制品只有冷却固化到一定刚性,脱模后(hòu)才能(néng)避免塑料制品因受到外力而产生变形。由于冷却时间(jiān)占整个成型周期约70%~80%,因此设计良好的(de)冷却(què)系统可以大(dà)幅缩短成型时间,提高注(zhù)塑生产(chǎn)率,降低成(chéng)本。设计不当的冷却系统会使成型时间拉长,增加(jiā)成本;冷却不均匀更会进(jìn)一步造成塑料制(zhì)品的翘曲变形。
根据实(shí)验,由熔体进入模具的热量大体分两部分散发(fā),一(yī)部分有5%经辐射、对流传递到大气(qì)中,其余95%从熔体传导到模具。塑料制(zhì)品在模具中由于冷却水管的作用,热量由模腔中的塑料(liào)通过热传导经(jīng)模架(jià)传至冷却水管,再通过热对流被冷却液(yè)带走。少数未被冷却(què)水带走的热量则继续在模具中传导,至接触外界后散溢于空气(qì)中。
注塑成型的成型周期由合模时间、充填时间、保压时间、冷却(què)时间及脱模时间组(zǔ)成。其中以冷却时间所占比重大,大约为(wéi)70%~80%。因此冷却(què)时间将直接影响(xiǎng)塑料制品(pǐn)成型(xíng)周期长短及产量大小。脱模阶段塑料制(zhì)品温度应冷却至低于(yú)塑料制品的热(rè)变形温度,以防止(zhǐ)塑料制品因残余应力导致的松弛(chí)现象或脱模外(wài)力所造成的翘曲及变形。
影响制品冷却速率的因素有:
塑料制品设计方(fāng)面。主要是塑料制品(pǐn)壁厚。制品厚度越大,冷却时间越(yuè)长。一(yī)般而言(yán),冷却时间(jiān)约与(yǔ)塑料制品厚度的平方成正比(bǐ),或是与(yǔ)大流道(dào)直径(jìng)的1.6次方成正比。即塑料制品厚度加倍,冷(lěng)却时间增加4倍。
模具材料及其冷(lěng)却方式。模具材料,包(bāo)括模具型芯、型腔材料以及(jí)模架材料(liào)对冷却速度的影响很大。模具材料热传导系数越高,单位时间内将热量从(cóng)塑(sù)料传递而出的效果越佳,冷(lěng)却(què)时间也越短。
冷却水管配置方式。冷却水管越靠近模腔,管径越(yuè)大,数目越多,冷却效(xiào)果越佳,冷却时间越短。
冷却液(yè)流量。冷却水(shuǐ)流量越大(一般以达(dá)到紊流为佳),冷却水以热对流(liú)方式(shì)带走热量的效果也越好。
冷(lěng)却液的性(xìng)质。冷却液的粘度(dù)